Simulation of laser-based welding in the automobile and machine tool sectors
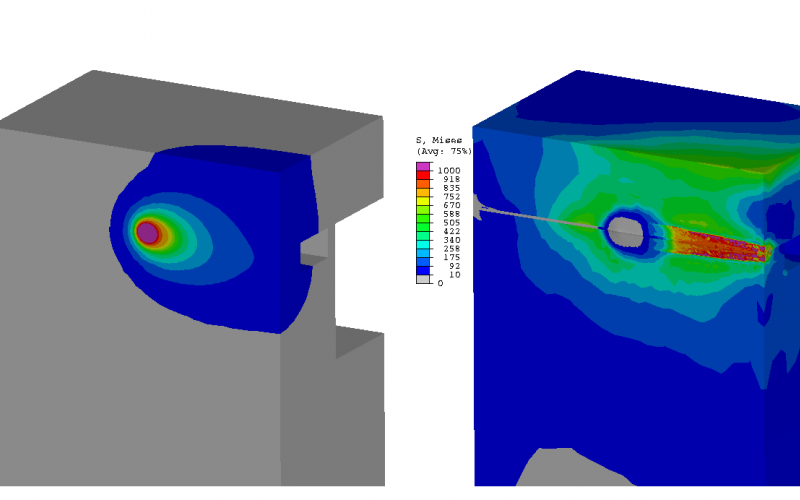
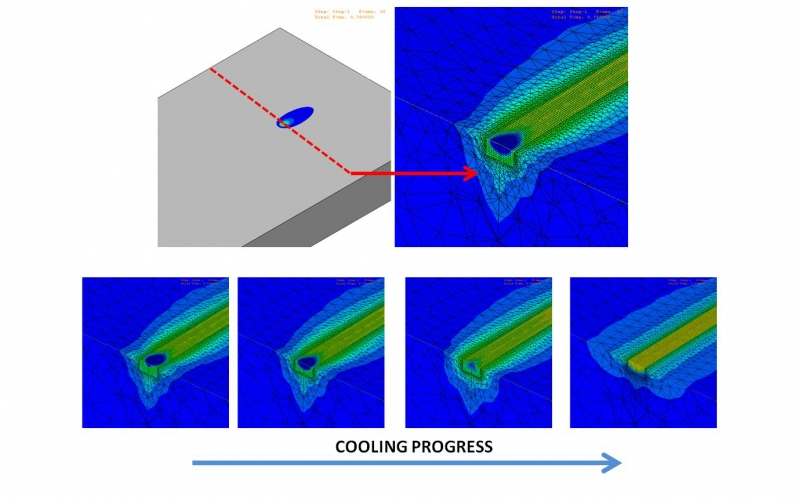
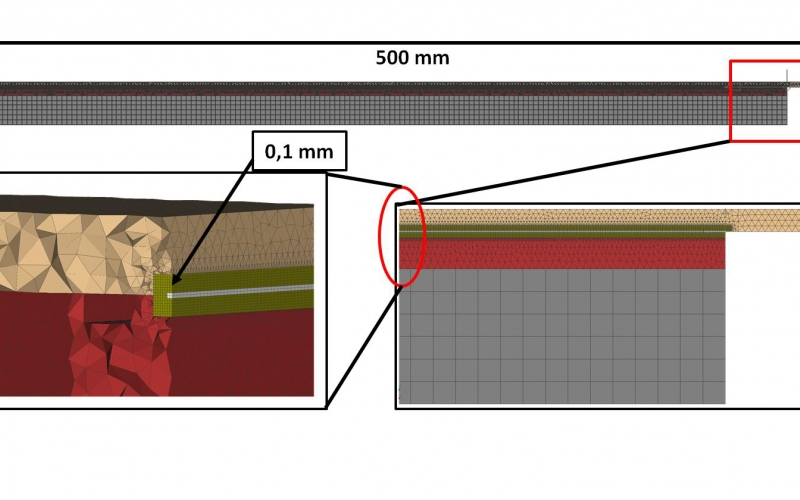
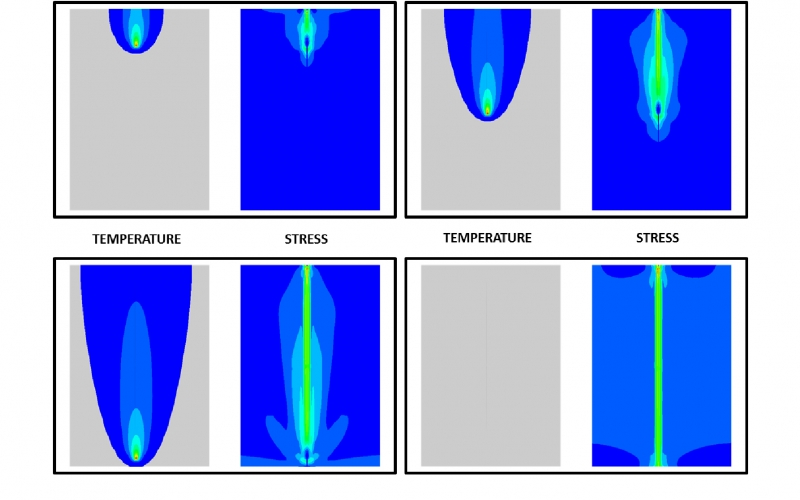
Lasersystemtechnik Bollinger & Ohr (LBO) is an SME founded in 1999, specialising in laser-welding technology. LBO offers a range of laser-welding services including the repair of dies and moulds, sheet-metal joining, surface coating and deep penetration welding and cutting. Many of the components of automobiles and machine tools are welded components which suffer thermally induced stress in the manufacturing process, resulting in flaws. The impact of these flaws on the durability of components needs to be assessed. Traditionally, welds have been assessed by physical inspection which involves the cutting, polishing and sanding of samples to obtain micro-sections. Such trials are costly and time consuming. Furthermore, the work piece under assessment is destroyed by this process. Simulation of the welding process, taking only a few hours on an HPC system, would dramatically reduce the time to assess and optimise a particular weld, thus avoiding expensive prototypes. However, to do this requires a suitable methodology for performing such simulations. The aim of this experiment was to determine and implement such a methodology.
The Challenge
The major advantages of simulations are the savings due to the avoidance of physical prototypes and the faster development cycle. Using simulations, initial results can be available within few hours rather than after days or weeks with prototypes. Models can be modified in order to find optimized welding parameters, such as feed rate, welding penetration depth and laser power. This can contribute dramatically to reducing costs and time. However, there are few, if any, simulation tools to model welding processes. This is because such processes are highly complex and difficult to observe. Accurate simulations require significant computing power due to the non-linear behaviour of materials and the highly transient conditions. These imply high levels of discretisation, resulting in very large models. SMEs simply cannot afford the necessary computer hardware to perform these simulations. In Fortissimo, SMEs have access to high-performance computing which can overcome this barrier by enabling the implementation of a suitable simulation tool. The challenge of this experiment was therefore to determine and implement such a tool.
The Solution
Lauer & Weiss (L&W), an expert in the development of software solutions for the automobile and machine tool industry, has developed a simulation of laser-welding processes based on the commercially available ABAQUS package. The accuracy of this methodology has been positively assessed through the physical inspection of welding samples in cooperation with LBO. This confirms that simulated welds accurately model real-world cases and that expensive physical prototypes can be eliminated.
The need to model temperature-dependent material properties and to resolve accurately the very fine scales of welds results in a large model requiring significant compute resources. Such resources are easily available, using Cloud-based HPC resources from HLRS, as are the necessary licences to use the ABAQUS package. LBO, L&W and HLRS are together making the simulation tool available as a service in the Fortissimo Marketplace, enabling customers both large and small to carry out simulations on a pay-per-use basis.
The Benefits
The cost of a physical prototype at LBO is ~€3.3K comprising materials (~€2K), staff costs (~€500) and microsections (~€800). Testing using a physical prototype takes ~1 week. However, using a physical prototype takes 3 or 4 trials costing in total ~€13K including ~€1.5K staff costs and a development time of ~3 weeks, which is quite long for urgent tasks.
In comparison, a computer-based analysis costs L&W €6K, comprising staff costs for 1 week of €4K for modelling, preparation of the computation, user subroutines and evaluation and one week of computing time (€2K for in-house cycle costs and licence fees). Results are available within two weeks. Once a running FEM model has been created, modifications to certain parameters are made very quickly, thus a second simulation loop is less expensive. The in-house cycle and licence fees remains at €2K, but the staff cost reduces to ~€500. Assuming that three simulations runs are necessary to find suitable welding parameters, the costs for the evaluation of a weld at L&W using HPC-based simulation are about €11K, which is almost the same as the physical weld trials at LBO with roughly the same development time. However, a complex calculation of a welding process would block all licences at L&W for seven days. This means that no other projects could be processed during this time, which is not acceptable.
The use of an HPC cloud at HLRS reduces the computing time to 24 hours. In this case, HLRS provides only the hardware environment and L&W brings its own licences. For L&W, the costs for the solver software per year are currently €80K for 24 ABAQUS licences. This is sufficient for using 40 cores in parallel for one calculation job. Increasing the costs for ABAQUS licenses by only 10%, L&W is able to run one FEM analysis with 80 cores at the HLRS. This reduces the computing time to less than 24 hours.
The staff costs for the first simulation remain at €4K and a further €500 for each simulation loop. However, the cycle and licence costs are reduced significantly to about €500. Assuming as before that three simulations loops are necessary, the costs for an HPC-based evaluation supported by HLRS can be reduced to about €5.5K, which is less than half the costs for physical weld trials at LBO.
In recent years, LBO has conducted four to five expensive welding trials per year. Using Cloud-based-HPC simulations, L&W can generate a significant cost reduction of ~40k EUR per year for these trials. For each new client like LBO, L&W sees a further benefit of €20K to €30K. In Germany alone there are several tens of such companies which gives L&W a significant potential for new business.
Companies Involved
End user: Lasersystemtechnik Bollinger & Ohr
HPC and Application expert: Lauer & Weiss GmbH
HPC Provider, Expert and Host Centre: HLRS, University of Stuttgart