Cloud-based design for the manufacture and simulation of high-performance composite structures
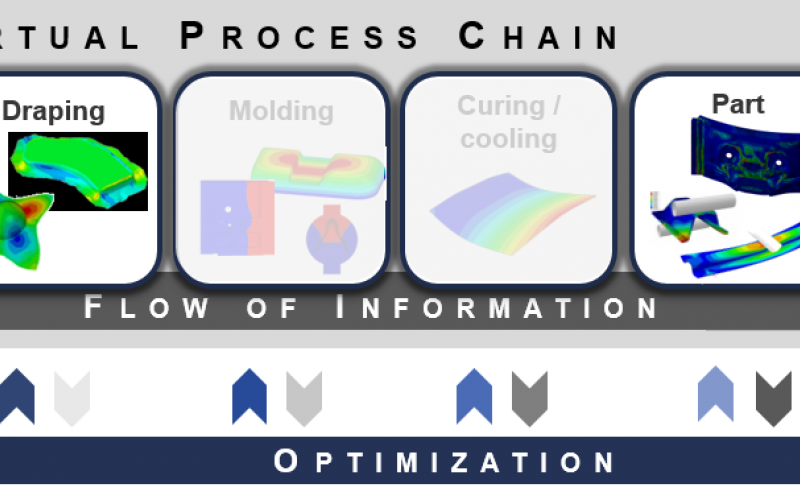
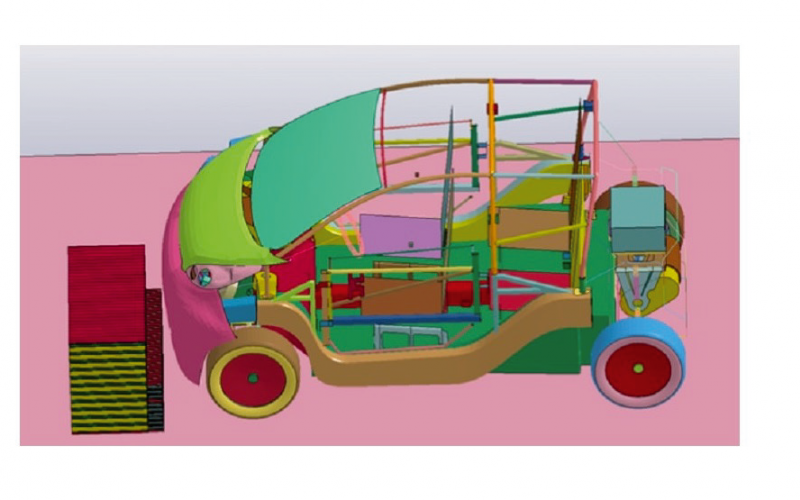
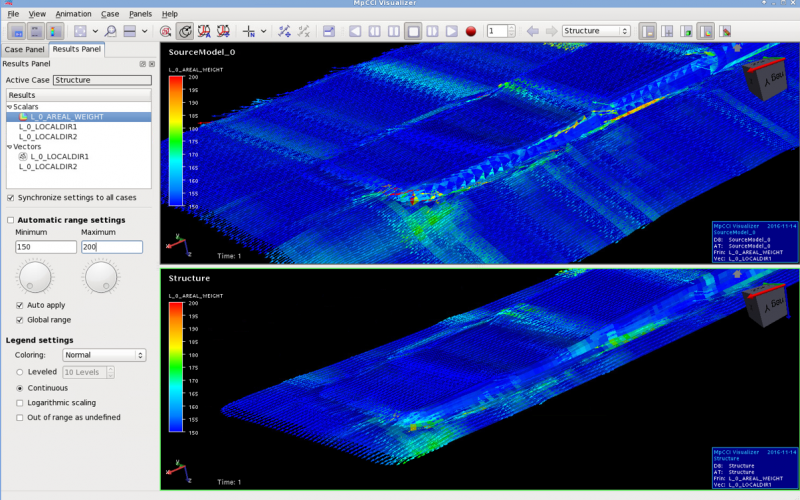
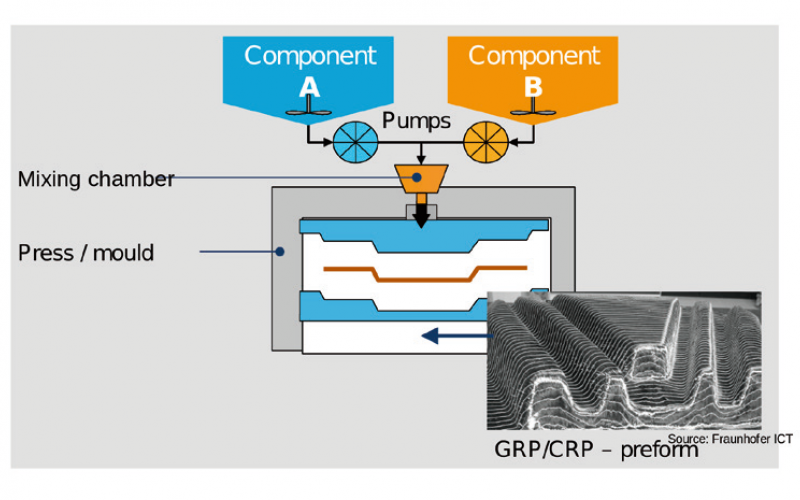
The industrial use of carbon-fibre-reinforced plastic (CFRP) is being driven by the increasing use of composites to reduce weight in the automotive industry, where cost and performance are major factors. Legislation around the world is increasing the requirement for lightweight vehicles. With world-wide tooling budgets running well into hundreds of millions of Euros, the simulation of processes and the prediction of manufacturing times are central to delivering high-quality products at an affordable price. Formtech Composites specialises in the design, engineering and manufacture of lightweight composites structures and components, using carbon, glass, aramid and other high-performance fibres. It collaborates with leading automotive, motorsport, military and aerospace partners to take forward composite research, engineering, prototyping and serialised manufacture. As a concrete example, Formtech produces inner bonnets for automotive vehicles. To maintain or improve its competitive position, Formtech has a clear need to use advanced simulation in its design process.
The Challenge
This experiment aimed to develop an integrated virtual process chain to simulate the manufacture of high‐performance composite structures. The objective of this CAE chain was to combine all essential simulation steps to enable integrated product development. Such a chain would firstly consider manufacturing effects from previous steps in the simulation and, secondly, allow an iterative structural optimisation over multiple simulation steps. To make high‐performance CFRP economically viable for large‐scale production, it is essential to reduce overall development and production costs. The big advantage of a continuous virtual CAE chain would be the acceleration of the development loops, with each single loop covering the simulation of manufacturing processes (draping, moulding and curing), the automated transfer of process simulation results, and the structural simulations of the product itself. The objective of this experiment was to develop a CAE chain which could tackle the reduction of overall development and production costs through the development of the required CAE chain and the implementation of the associated development loops.
The Solution
KIT in cooperation with Fraunhofer SCAI has developed a prototype simulation platform, which allows the planning of the manufacturing processes and the prediction of final structural performance. This enables the required holistic product optimisation. In this experiment an integrated workflow to optimise the design of CFRP components has been developed, which uses the prototype from KIT and Fraunhofer SCAI. It is accessible through a web‐based interface and runs on a Cloud-based-HPC system at Gompute. Even though this approach requires significant compute resources for the design of components, such as an inner bonnet, the Gompute system can easily satisfy the necessary compute requirements.
The Benefits
The platform developed increases the quality of designs. It adds functionality while reducing the work load on the engineer’s side. It shortens simulation times from days to hours whilst offering more detailed simulations. Such simulations lead to less material usage and the need for fewer mechanical tests. Formtech has already exploited the HPC capacity of Gompute to meet a project deadline where a 50% reduction in compute time was imperative. Clearly advanced simulation enables Formtech to maintain a competitive edge over other companies world-wide. As a result of using advanced simulation, Formtech anticipates an increase in revenue per annum of ~€100K. KIT estimates that, due to time saving through using HPC systems, it will increase its annual revenues by around €30K. Additionally, annual personnel costs will be reduced by €10K. Fraunhofer SCAI expects a strongly growing demand for customised and integrated CAE development. Fraunhofer SCAI estimates that, during the next 2 to 3 years, it can increase its regular annual licence revenues for such developments by ~€60K The outcome of this experiment has given valuable feedback to Gompute. The success of this CAE chain implementation has already brought new business with annual turnovers of over €2K for the sale of compute cycles. KIT and Fraunhofer SCAI plan to offer a CFRP simulation service via the Fortissimo Marketplace starting in Q3 2017.
Companies Involved
End-user: FORMTECH COMPOSITES
ISV: FRAUNHOFER SCAI
Domain Expert: KIT-FAST
HPC: Provider: GOMPUTE