Cloud-based optimisation in the cutting of steel reinforcements
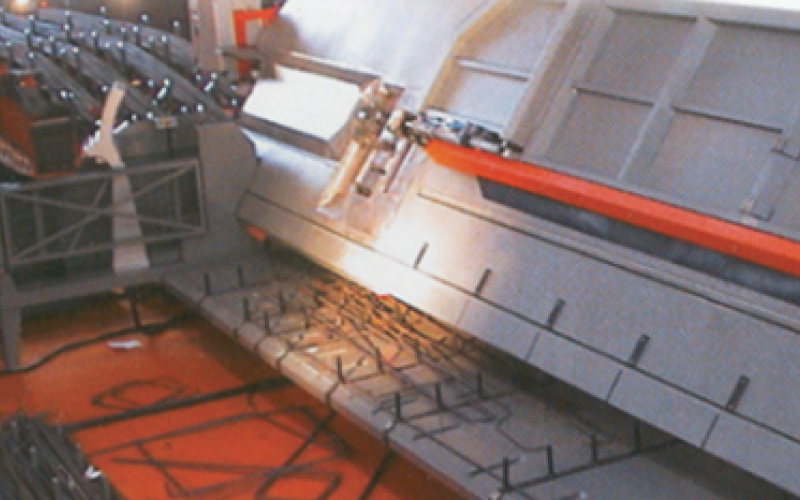
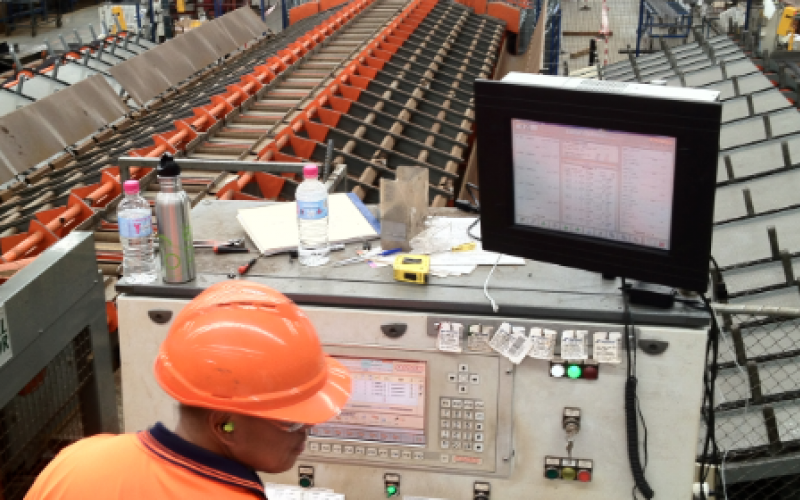
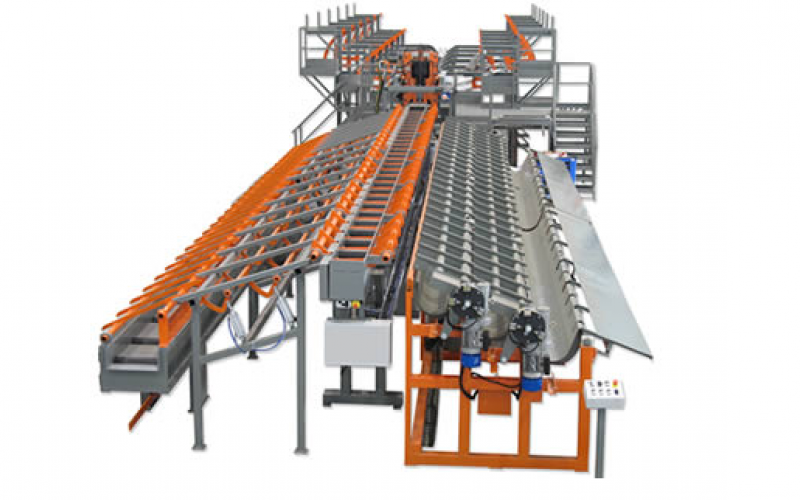
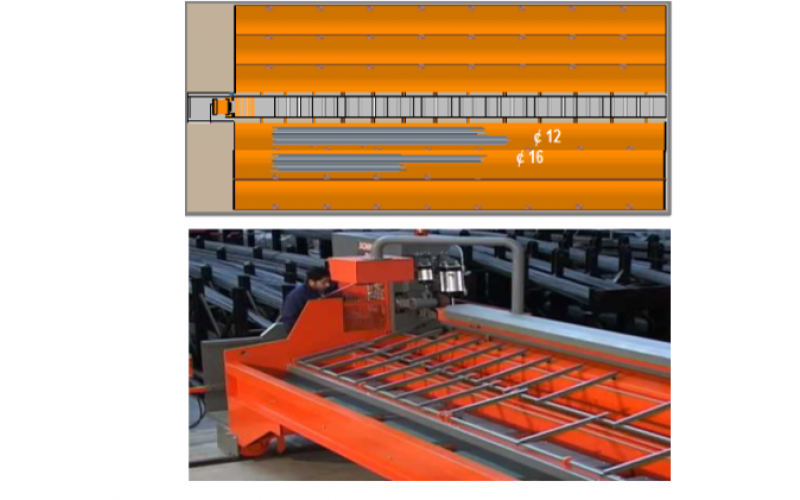
Schnell Software, a Spanish SME, designs specialized CAD-CAM software for companies which cut and bend steel. In particular, it develops software applications which optimise the cutting of iron bars for reinforced concrete. SCHNELL already had optimisation software which ran on a PC. For medium-sized orders with lower levels of optimisation, SCHNELL could get results on a PC in around 10 minutes. However, execution on a PC could take several hours if the level of optimization were increased. Big orders, which needed high levels of optimisation, could take more than 3 hours, which is impractical in a production environment. The optimisation of cutting and bending of iron bars is based on complex algorithms which are numerically intensive. Good optimisations would enable SCHNELL’s customers to plan their schedules to obtain the best possible combination of its orders, to minimise wastage in the cutting and bending process and to save time in the analysis of production orders and raw material requirements.
The Challenge
The challenge facing SCHNELL was to modify its software to run on a Cloud-based HPC system rather than on a local PC. The objective was to reduce the compute time from hours down to minutes for even large-scale optimisations. A further goal was to develop a graphical user interface to steer the optimisations. The modified software would serve as a database portal to optimize functions in the Cloud and clients would be able to carry out a real simulation of a cutting process with minimal cost and effort.
For small companies, the acquisition of an in-house optimization system that guarantees a reliable cut of high quality requires an initial economic investment in hardware and software. Not all small and even large companies, are willing to do this because they are not sure of the benefits. Through the implementation of a cloud-based optimisation service on a pay-per-use basis this barrier can be overcome because companies are able to test and evaluate the service without the need for a large capital investment.
The Solution
The optimization software has been adapted to run in a distributed Cloud-based HPC infrastructure. Through the use of a graphical user interface it is easy to setup and optimise bar cutting and bending optimisations. This hides all the complexity of the Cloud. Launching optimisations is as simple as sending some input files, with appropriate parameters and receiving the results after a manageable processing time.
The Benefits
A large foundry produces 2,000 tonnes of steel bars per month. Through the use of Cloud-based high-level optimisation, it can reduce waste steel by 2% (480 tonnes per annum) Given that the average price of steel is €500 per tonne, this represents a saving of €240K per annum. This compares with a saving of only €60K per annum using only low-level optimisations on a PC. Additionally, by using high-level optimisations there is an associated reduction in personnel costs of €30K per annum.
A simple analysis of the costs of performing the high-level optimisation in-house on a sufficiently powerful system results in a yearly expenditure of €80K. The corresponding computing costs of performing the same optimisation in the Cloud are only €7.5K per annum.
Over the next 5 years SCHNELL estimates a total income of ~€480K from the provision of its Cloud-based optimisation service to steel foundries, including Cloud-computing and SCHNELL licence costs, resulting in a total profit of ~€440K. In addition to this, CESGA will increase its sales of computer cycles by around 175,000 CPU hours per year. It will also use the outcome of this experiment as a reference to promote its Cloud Services.
Companies Involved
End user and ISV: Schnell Software S.L.
HPC and Application expert: Universidad de Zaragoza - BIFI
Independent Software Vendor: Schnell Software S.L.
HPC Provider, Expert and Host Centre: CESGA