Cloud-based design of ultra-clean containers for high-purity chemicals
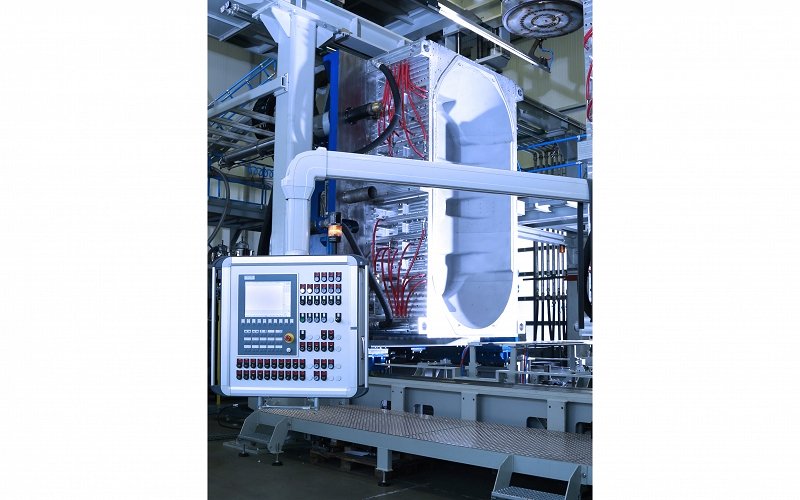
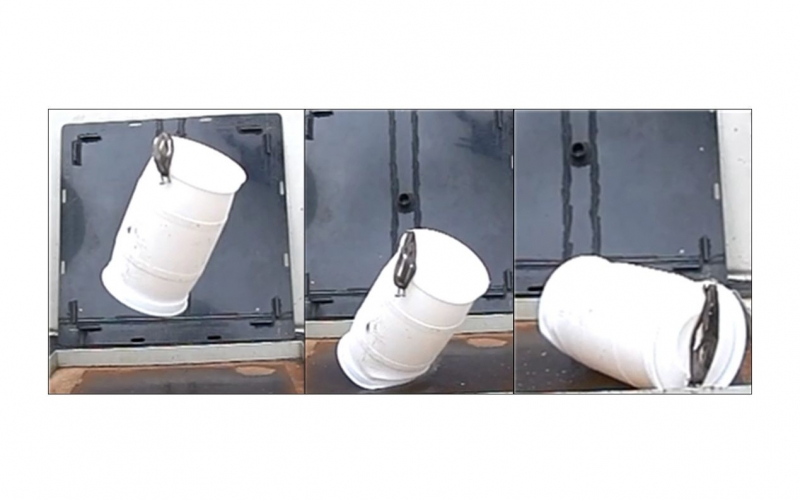
Rikutec is a German SME active in the blow moulding of plastic containers. Its core business is both the manufacture of large installations and the supply of complete turnkey facilities for blow-moulded products. Rikutec’s customers are from the chemical and petrochemical foodstuffs and pharmaceutical sectors. In these sectors ultra-clean containers are essential in the supply of high purity chemicals. To maintain and extend its leading market position Rikutec needs more reliable and more efficient design methods with faster response times. Rikutec has already started to work with partners to evaluate the benefits of numerical simulation in blow-moulding. This work will be taken forward in this experiment whose goal is to create a new simulation service which can be used by companies such as Rikutec to develop new products in a shorter time. Rikutec expects that dedicated blow-moulding simulation services on HPC-systems will lead to lower costs, increased product quality and a more efficient development processes. Fraunhofer SCAI (Germany) is a non-profit R&D institute which provided the expertise in software development. Hagen Stiftung and Hagen Engineering, both from Germany, are domain experts in plastic parts and blow moulded articles. Accuform is a Czech software manufacturer. One of their products is the process simulation software B-SIM. Gompute (Sweden) provided the HPC resources and expertise.
The Challenge
Extrusion blow moulding is the standard manufacturing method for hollow plastic parts such as bottles, cans, fuel tanks and large containers. A specific example is ultra-clean containers for the microelectronic device industry.
Companies that manufacture these products need faster, more reliable, and more efficient design methods.
Before this experiment, automated optimization was not possible. The individual design and simulation steps had to be carried out manually. The simulations were performed on standard workstation systems, with one single design loop taking up to 2 days.
The Solution
The partners have developed a standardized and automated workflow incorporating different simulation tools so that manual intervention is no longer necessary. This involved extension to the multi-physics interface software MpCCI from Fraunhofer. Through utilization of cloud-based HPC and parallelization of the simulation, the time required to create a new design can be reduced significantly.
The combination of this new workflow and the use of HPC means the automated simulation of blow moulded parts is possible for the first time.
As a result, the development times have been shortened and more design variants can be tested in the same time. Additionally, expensive physical moulds are needed less, and material usage is reduced, further lowering the cost of manufacture.
Business Impact
RIKUTEC will benefit from this experiment as it will have access to more reliable and more efficient design methods with faster response times. The number of (physical) design loops can be reduced, and the quality of products is enhanced. Through the application of simulation methods, substantial cost savings have been made in the development process.
Hagen Engineering will use the experiment results to expand its market position as a provider of simulation services. It expects more companies to use CAE-methods in the design process of plastic parts in the near future, so access to an automated, integrative CAE workflow will make them more competitive.
The extension of its multi-physics software solution will help Fraunhofer to find further customers in the plastic moulding domain. Over the next 2-3 years Fraunhofer expects 5-10 new users with licence revenues of €30,000 to €60,000 per year. In the medium term, Fraunhofer expects to see a rapidly increasing market for integrated manufacturing simulation solutions. Interface tools like the MpCCI Mapper will benefit from that market growth.
Benefits
For RIKUTEC, the benefits are:
- Reduced costs for each design loop can amount > € 20,000.
- Optimization of item weight could reduce the total costs by several thousand euros per year.
- Through the utilization of HPC, computation times are shortened by a factor of 4x – 5x.
Organizations involved
End User: Rikutec
HPC Expert: Fraunhofer SCAI
ISV: Accuform
Application Centre: Hagen Stiftung
Engineering Service Provider: Hagen Engineering
HPC Provider: Gompute