The Virtual Engineer 2 – Cloud Based Optimisation of Production in the Dairy Sector
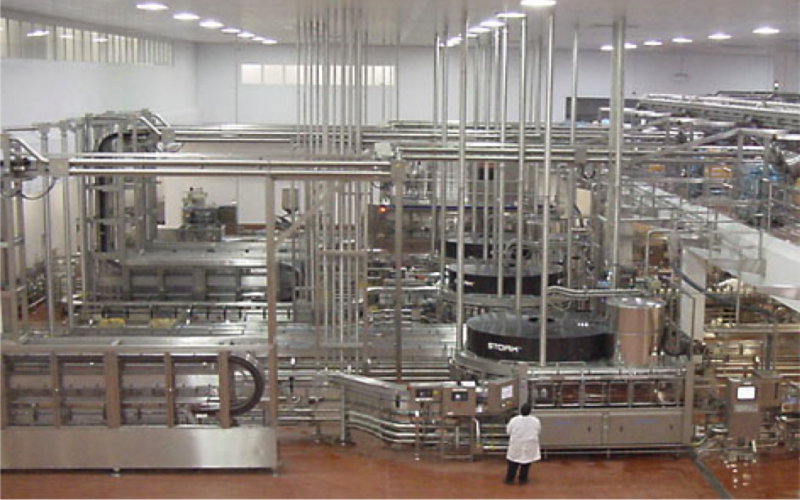
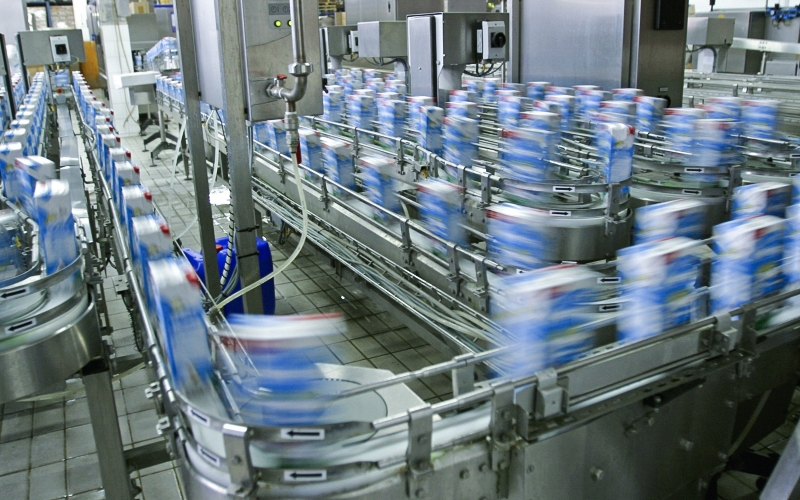
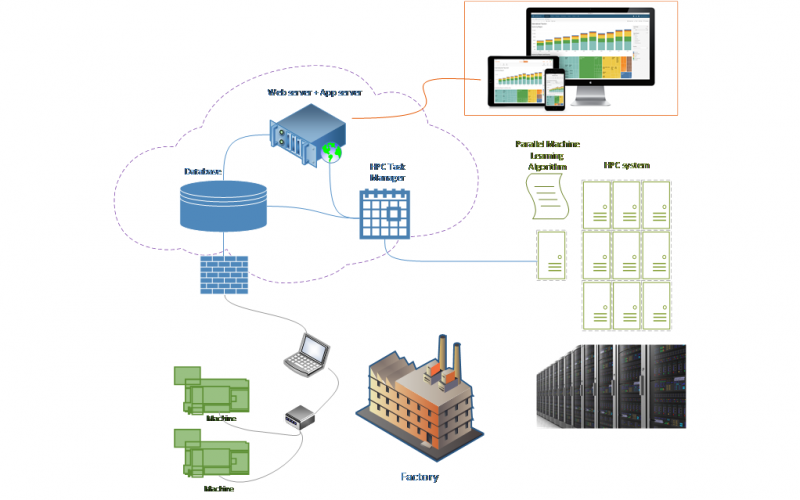
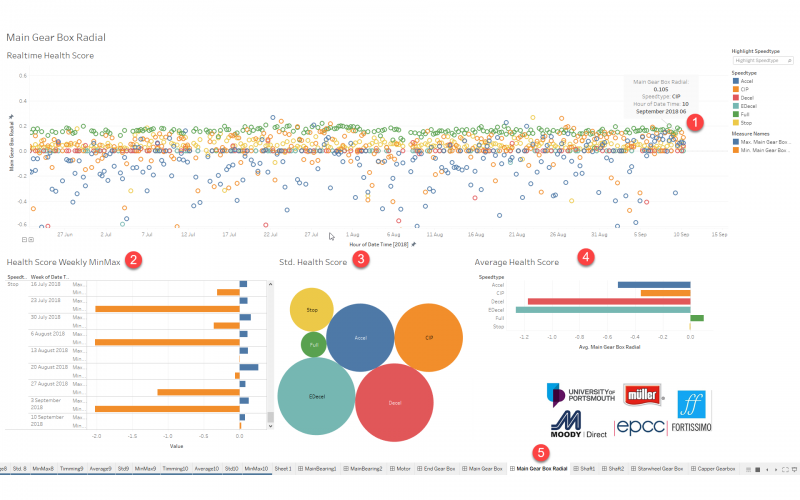
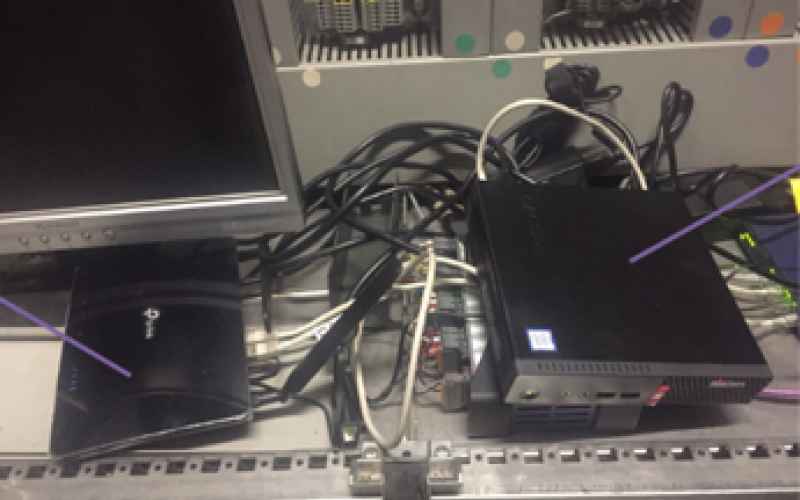
MOODY DIRECT (End User) is a British SME that manufactures bespoke components both manually and with the latest CNC machinery to support servitisation of Original Equipment Manufacture (OEM) machines in a range of industries. The large dairy company Müller is one of its major customers. THE UNIVERSITY OF PORTSMOUTH (Application Expert) was the domain expert in this experiment. EPCC (HPC Centre) provided HPC resources and expertise.
The Challenge
The Dairy industry is a low-margin, high turnover industry. Machines can break down up to 3-5 times per year with a breakdown lasting up to 6 days at a time. Annual breakdowns can cost up to €11.4m per machine annually as penalty fines for non-supply, lost milk, clean-up costs and environmental fines can cost the customer up to €380,000 per day.
Moody Direct is an SME that delivers a maintenance service into large dairy production sites and whilst there are some predictive maintenance measures in place already, they are not comprehensive and not multi-machine, multi-site. Moody wants to offer enhanced Service Agreements with UK customers to reduce downtime and achieve increased sales through supply and manufacture of spares.
The Solution
This experiment developed predictive maintenance software as a service solution to Moody for machines at Müller UK & Ireland Ltd. Data collection, management and transfer was developed by the University of Portsmouth and supported by EPCC for full analysis in near real-time direct from the production site. A GUI client was developed for Moody Direct Ltd’s mobile engineers that connects seamlessly to the HPC system showing real time information to aid decision-making. HPC was exploited for the high-performance data analytics. This made refinement of the algorithms much quicker, and facilitated near real time analysis of data. This was used to create the predictive maintenance platform (Software as a Service) for users in a cloud-based online system. Without HPC, this would not be possible.
Business Impact
Moody Direct now has access to a working online platform that will give it oversight of the machines on the Müller site. Currently the system is only streaming data from 1 machine, but there are 3 other machines onsite that can in future share their data with the online platform. This means Moody Direct can now begin to offer an enhanced service-based business model which is anticipated to bring better management of the scheduling of engineers and control of stocks of spare parts. The platform will also improve the capability and knowledge of the Moody Direct Engineers and increase their productivity as a result.
For Müller, the benefits are increased productivity (fewer breakdowns mean more output) and energy minimisation due to improved machine health. There will also be a reduction in food waste as machines continue to run successfully without the need to dispose of lost milk during machine failure.
For the University of Portsmouth the experiment has led to the generation and transfer of knowledge within its Operational Research and Artificial Intelligence academic community and an improved knowledge of big data analytics and parallel processing through HPC.
Benefits
- Savings for dairy manufacturers in excess of €50m as penalty fines are avoided
- Increased productivity of production lines through operational optimisation by up to 30 days per machine per year which equates to approximately 200,000 bottles per machine per year.
- Reduction in environmental contamination and food waste: up to 200,000 bottles worth of milk saved from disposal per machine.
Organizations Involved
End User: Moody Direct
Application Expert : University of Portsmouth
HPC Provider: EPCC